Watch the video of this application at the bottom of this page.
A recent prospect reached out to the FlexArm team looking for a better tapping solution. The company is a nationally-ranked advanced facade contractor, and they were looking for an efficient way to tap aluminum extrusions.
They are currently outsourcing these parts or tapping them in-house with a drill press. However, the problem with outsourcing is that they have no control over the quality or consistency of their parts. Because their volume is so high, they were hoping to leave the drill press for a quicker and more efficient option. We told them to send in some of their parts and we would test them using the FlexArm.
The extrusion needs two inches of total thread depth and needs to accept a set screw at the end. We fixtured up the part horizontally and chose to tap with the GHM-18 Hydraulic FlexArm. The multi-position head (signified with the ‘M’ in GHM) will allow the operator to tap horizontally and easily reach their desired thread depth.
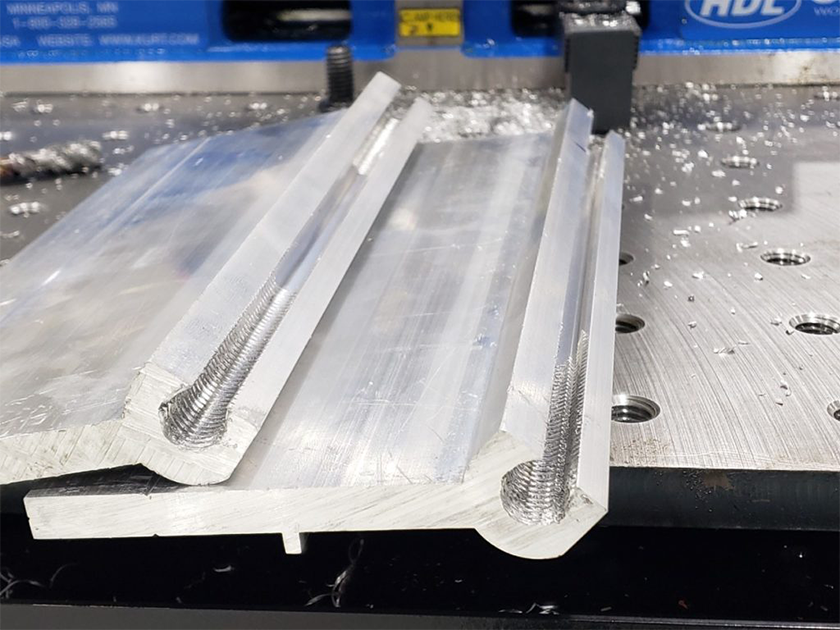
One issue we ran into during this tap test was chip evacuation. The end-user supplied us with a straight flute pulley tap, but due to the horizontal positioning, the chips had nowhere to go. We swapped the tap with a 3 flute spiral point tap, and this helped to pull the chips out of the part. The tap change was a success and the FlexArm had no problem tapping the aluminum extrusion to the correct depth.
If you are experiencing any similar problems or just looking to speed up your tapping process give us a call at 1-800-837-2503 or schedule a tap test today.